技術開発ニュース No.168
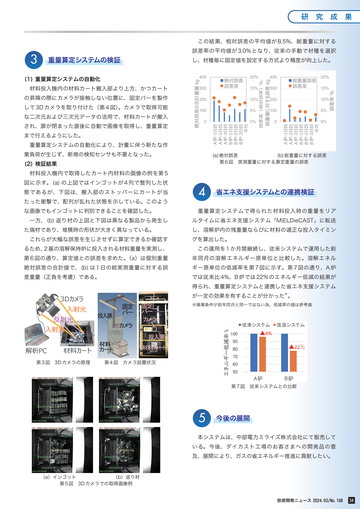
- ページ: 35
-
研 究 成 果
この結果、相対誤差の平均値が 8.5%、総重量に対する
(1) 重量算定システムの自動化
し、材種毎に固定値を設定する方式より精度が向上した。
400
20%
15%
300
15%
200
10%
200
10%
100
5%
100
5%
0
0%
0
0%
20%
300
の昇降の際にカメラが接触しない位置に、固定バーを製作
して 3D カメラを取り付けた(第 4 図)。カメラで取得可能
な二次元および三次元データの活用で、材料カートが搬入
され、扉が閉まった直後に自動で画像を取得し、重量算定
まで行えるようにした。
重量算定システムの自動化により、計量に伴う新たな作
業負荷が生じず、新規の検知センサも不要となった。
(2) 検証結果
A炉-1日目
A炉-2日目
A炉-3日目
B炉-1日目
B炉-2日目
B炉-3日目
材料投入機内の材料カート搬入部より上方、かつカート
kg
400
A炉-1日目
A炉-2日目
A炉-3日目
B炉-1日目
B炉-2日目
B炉-3日目
重量算定システムの検証
kg
3
誤差率の平均値が 3.0% となり、従来の手動で材種を選択
(a) 絶対誤差 (b) 総重量に対する誤差
第 6 図 実測重量に対する算定重量の誤差
材料投入機内で取得したカート内材料の画像の例を第 5
図に示す。(a) の上図ではインゴットが 4 列で整列した状
態であるが、下図は、搬入部のストッパーにカートが当
たった衝撃で、配列が乱れた状態を示している。このよう
4
省エネ支援システムとの連携検証
な画像でもインゴットに判別できることを確認した。
重量算定システムで得られた材料投入時の重量をリア
一方、(b) 返り材の上図と下図は異なる製品から発生し
ルタイムに省エネ支援システム「MiELDieCAST」に転送
た端材であり、堆積時の形状が大きく異なっている。
し、溶解炉内の残重量ならびに材料の適正な投入タイミン
これらが大幅な誤差を生じさせずに算定できるか確認す
グを算出した。
るため、2 基の溶解保持炉に投入される材料重量を実測し、
この運用を 1 か月間継続し、従来システムで運用した前
第 6 図の通り、算定値との誤差を求めた。(a)は個別重量
年同月の溶解エネルギー原単位と比較した。溶解エネル
絶対誤差の合計値で、(b) は 1 日の総実測重量に対する誤
ギー原単位の低減率を第 7 図に示す。第 7 図の通り、A 炉
差重量(正負を考慮)である。
では従来比 4%、B 炉では 22% のエネルギー低減の結果が
得られ、重量算定システムと連携した省エネ支援システム
3D
が一定の効果を有することが分かった※。
※操業条件が前年同月と同一ではない為、低減率の値は参考値
PC
第 3 図 3D カメラの原理 第 4 図 カメラ設置状況
第 7 図 従来システムとの比較
5
今後の展開
本システムは、中部電力ミライズ株式会社にて販売して
いる。今後、ダイカスト工場のお客さまへの開発品の普
及、展開により、ガスの省エネルギー推進に貢献したい。
(a)インゴット (b)返り材
第 5 図 3D カメラでの取得画像例
技術開発ニュース 2024.03/No.168
34
- ▲TOP